Mastering Industrial Vacuum System Design: A Comprehensive Guide
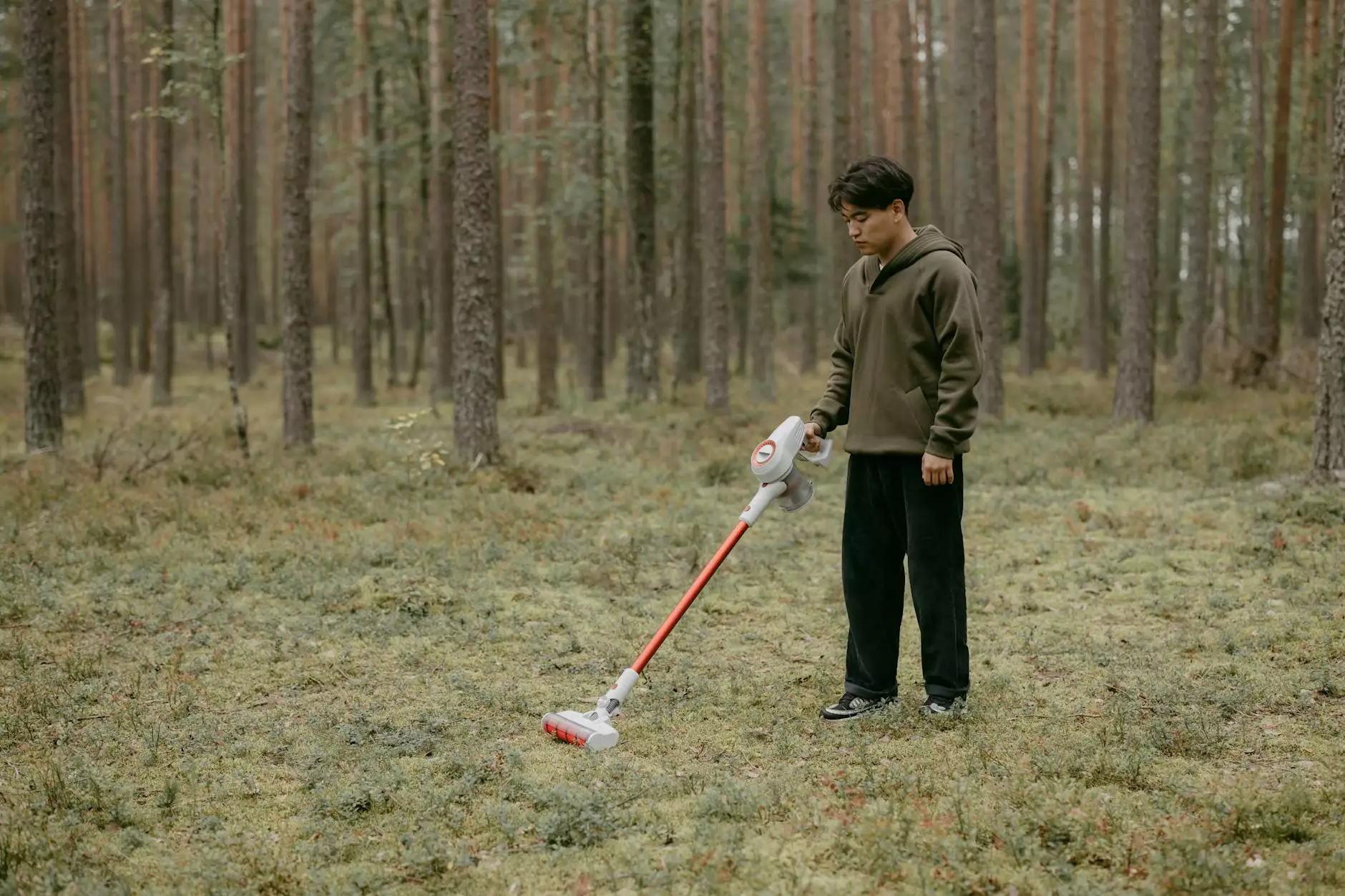
Industrial vacuum system design is a critical aspect of modern manufacturing and processing operations. Whether you're in automotive, pharmaceuticals, or food processing, understanding the nuances of these systems not only improves efficiency but also enhances overall production quality. This article dives deep into the fundamentals of industrial vacuum systems, their design principles, and their importance for businesses today, particularly within categories like Blow Dry/Out Services.
The Fundamentals of Industrial Vacuum Systems
At its core, an industrial vacuum system is designed to remove air and other gases from a sealed volume. This process creates a vacuum which can be applied to various tasks such as material handling, drying, and conveying. The essence of industrial vacuum system design lies in its ability to maximize efficiency while ensuring safety and reliability.
Key Components of Industrial Vacuum Systems
Understanding the components of an industrial vacuum system is crucial for effective design. Here are the primary components:
- Vacuum Pumps: The heart of the system, responsible for removing air and creating the vacuum. There are several types, including rotary vane, diaphragm, and positive displacement pumps.
- Vacuum Chambers: Enclosures that hold the material or product being processed. Their design must consider material compatibility, pressure handling, and spatial efficiency.
- Piping and Fittings: The conduits that transport air and materials in and out of the vacuum chamber. Proper sizing and materials are essential to maintain system efficiency.
- Filters: Used to trap particulates and contaminants, protecting the vacuum pump and ensuring product quality.
- Control Systems: Automated systems that regulate vacuum levels and monitor performance. These systems enhance user convenience and operational safety.
Why Industrial Vacuum Systems Matter
Industrial vacuum systems are not just about creating a void; they play a pivotal role in enhancing operational efficiencies. Their importance includes:
- Efficiency Improvements: A well-designed vacuum system can significantly speed up drying and processing times, leading to faster turnaround times.
- Quality Control: By removing pollutants and moisture, vacuum systems help maintain the integrity of products throughout the manufacturing process.
- Cost Savings: Reducing processing times and minimizing waste leads to substantial cost savings in labor and materials.
- Environmental Benefits: Effective vacuum systems contribute to a cleaner work environment by minimizing airborne contaminants and ensuring proper handling of waste materials.
Design Considerations for Industrial Vacuum Systems
When it comes to industrial vacuum system design, several factors should be considered to ensure optimal performance. These include:
1. Application Requirements
Different applications require different vacuum levels, flow rates, and material handling attributes. Understand the specific needs of your operation to design an effective system.
2. System Layout
The layout of the vacuum piping and pump arrangement can drastically affect system efficiency. Reduced bends and shorter runs minimize resistance and enhance performance.
3. Energy Efficiency
Energy consumption is a significant factor in industrial operations. Opt for energy-efficient pumps and control systems to reduce operational costs and environmental impact.
4. Material Compatibility
Choose materials for the vacuum system that are compatible with the substances being processed. This is crucial for preventing contamination and ensuring system longevity.
5. Safety and Regulatory Compliance
Ensure that your vacuum system complies with all relevant safety and environmental regulations. Implementing safety features can also help protect workers and equipment.
Implementing Industrial Vacuum System Design in Blow Dry/Out Services
In categories like Blow Dry/Out Services, the application of industrial vacuum systems takes on a unique form. These systems help streamline the drying processes after washing products or during the finishing stages of manufacturing.
Benefits Specific to Blow Dry/Out Services
Utilizing industrial vacuum systems for blow drying entails several benefits:
- Improved Drying Time: Vacuum drying can drastically reduce moisture content in products which is essential in ensuring quality and extending shelf life.
- Uniform Results: Maintaining consistent vacuum conditions ensures uniform treatment across all products, preventing undercooked or overcooked materials.
- Reduced Product Damage: Gentle vacuum drying reduces the risk of mechanical damage often associated with air blow drying methods.
Case Studies: Successful Industrial Vacuum System Applications
To illustrate the effectiveness of well-designed industrial vacuum systems, consider the following case studies:
Case Study 1: Pharmaceutical Company
A leading pharmaceutical manufacturer faced challenges with moisture retention in their products. By redesigning their vacuum system to incorporate rotary vacuum pumps and optimized piping arrangements, they reduced drying times by 50%, resulting in a significant increase in production capacity and a decrease in operational costs.
Case Study 2: Food Processing Plant
In a food processing facility, implementing an industrial vacuum system for blow-drying fruits led to enhanced product quality. The use of vacuum systems allowed the company to achieve a moisture content of less than 5% while maintaining flavor and nutritional integrity.
The Future of Industrial Vacuum System Design
The future of industrial vacuum system design is promising, with ongoing advancements in technology improving efficiency and capability. Here are some trends to watch:
- Smart Technology Integration: IoT-enabled systems that monitor performance, predict failures, and streamline maintenance.
- Energy Efficiency Innovations: New materials and designs that reduce the environmental impact of vacuum systems.
- Advanced Materials: The use of composite materials for pumps and chambers that enhance durability while reducing weight and costs.
Conclusion: Why Choose Expert Industrial Vacuum System Design
Choosing the right industrial vacuum system design is not just about picking a machine; it’s about optimizing your entire manufacturing process. From improving drying efficiency in Blow Dry/Out Services to ensuring quality control in pharmaceuticals, the implications are vast. Investing in the right design can yield significant benefits, enhancing productivity and minimizing costs. As technology evolves, staying informed and adapting will be the key to maintaining a competitive edge in any industry.
For more information on achieving optimal industrial vacuum system design tailored to your needs, visit tmm.com.tr.