Understanding Membranes for Vacuum Presses: An Essential Guide
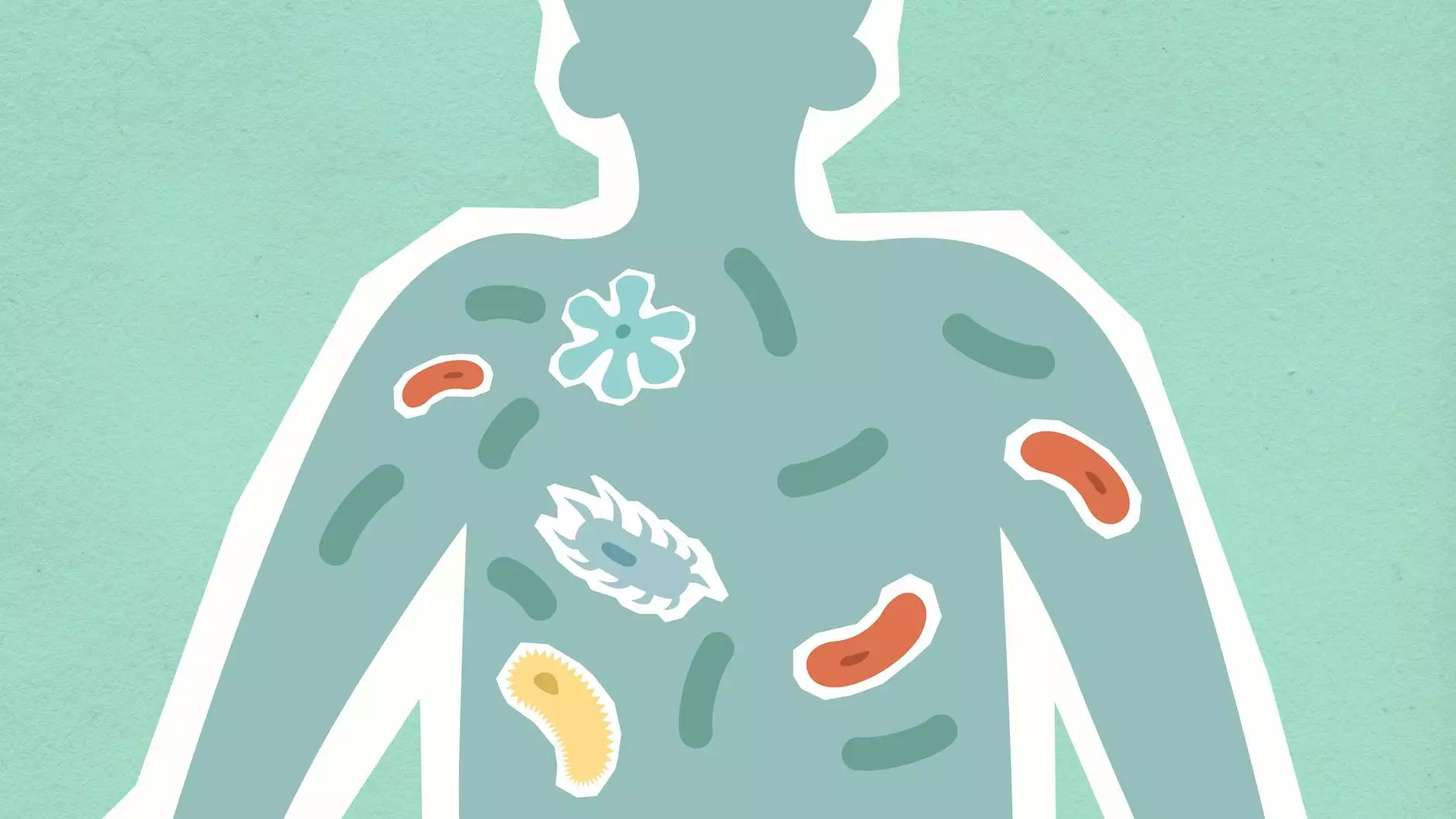
Membranes for vacuum presses are indispensable components in various industrial applications. From the health & medical sectors to the beauty & spas industries, these membranes play a critical role in ensuring efficiency and product quality. This comprehensive article delves deeper into the various aspects of these membranes, exploring their benefits, types, applications, and how they contribute to enhancing overall productivity.
What Are Membranes for Vacuum Presses?
Membranes for vacuum presses are flexible sheets made from durable materials, such as silicone, rubber, or other synthetic compounds. They create a vacuum seal, allowing for the efficient compression of materials and ensuring even pressure distribution during the pressing process. The unique properties of these membranes significantly influence the quality and effectiveness of the products being manufactured.
Key Benefits of Using Membranes in Vacuum Presses
- Enhanced Product Quality: Using high-quality membranes ensures consistent pressure, leading to better adhesion and fewer defects in finished products.
- Improved Efficiency: Proper membrane selection reduces processing times, optimizing overall workflow in manufacturing processes.
- Cost-Effectiveness: Investing in durable membranes reduces the frequency of replacements and maintenance costs.
- Versatility: Membranes can be tailored to suit various applications and materials, ranging from soft woods to complex composites.
Types of Membranes for Vacuum Presses
Understanding the different types of membranes for vacuum presses is crucial for selecting the right one for your specific application. Here’s a detailed overview of common types:
1. Silicone Membranes
Silicone membranes are widely used due to their flexibility, heat resistance, and excellent tensile strength. They are highly durable, ensuring long-lasting performance even under extreme conditions. Additionally, silicone membranes are non-stick, which helps in preventing material from adhering to the membrane surface.
2. EPDM Membranes
Ethylene Propylene Diene Monomer (EPDM) membranes are known for their excellent weather resistance and durability. They perform well under varying temperatures and can withstand exposure to aging, ozone, and UV radiation. This makes them suitable for outdoor applications.
3. Neoprene Membranes
Neoprene membranes offer excellent chemical and oil resistance, making them ideal for industries that deal with volatile substances. They provide a good balance between flexibility and strength, ensuring an effective pressing process.
4. Rubber Membranes
Rubber membranes are commonly used in industrial applications due to their cost-effectiveness and versatility. They can be manufactured to various thicknesses and hardness levels, making them suitable for diverse uses.
Applications of Membranes for Vacuum Presses
Membranes for vacuum presses find applications in several industries, each requiring specific qualities for best performance. Here are some notable sectors:
1. Health & Medical Industry
In the health and medical sectors, the need for precision and cleanliness is paramount. Membranes used in these contexts must be manufactured from materials that meet strict health standards. They are crucial in the fabrication of medical devices, ensuring sterile environments during the molding processes.
2. Beauty & Spas
The beauty and spa industries utilize membranes for creating bespoke products, such as custom massage tables, facial masks, and other spa equipment. The tactile properties of the membranes should also be taken into account to enhance client comfort.
3. Medical Spas
Medical spas often require membranes that can withstand specific pressures while maintaining aesthetic quality. The versatility of membranes for vacuum presses allows for the production of high-quality cosmetic devices that require vacuum sealing.
Choosing the Right Membrane for Your Vacuum Press
Selecting the appropriate membrane for your vacuum press involves several considerations:
1. Material Compatibility
Ensure that the membrane material is compatible with the materials being processed. For example, if working with resins, a non-stick silicone membrane might be the best option.
2. Thickness and Durability
Consider the operating conditions of the vacuum press, including temperature and pressure levels, to choose the right thickness and durability for the membrane.
3. Cost vs. Quality
While it may be tempting to choose lower-cost options, investing in high-quality membranes can result in long-term savings through reduced replacements and improved product quality.
Maintenance Tips for Vacuum Press Membranes
Proper maintenance of membranes for vacuum presses extends their lifespan and enhances their performance. Here are some essential tips:
1. Regular Cleaning
Clean the membranes regularly to remove any residue, oils, or materials that could affect adhesion in future uses. Use non-abrasive cleaners to prevent damage.
2. Inspect for Damage
Before each use, inspect the membranes for any signs of wear, tears, or punctures. Address any issues immediately to prevent compromise during the pressing process.
3. Store Properly
Store membranes in a cool, dry place away from direct sunlight. Proper storage can prevent premature aging and material degradation.
The Future of Membranes for Vacuum Presses
The membranes for vacuum presses market is poised for growth, driven by advancements in material technologies. Emerging materials promise to deliver superior functionality, including enhanced resistance to chemicals and temperatures. Additionally, the integration of smart technologies may lead to membranes that can self-regulate pressure or offer feedback on performance.
Conclusion
In conclusion, membranes for vacuum presses are crucial components across various industries, delivering unique benefits that enhance productivity and product quality. Selecting the right membrane, maintaining it properly, and staying abreast of industry advancements are key strategies for businesses in the health, beauty, and medical sectors. To optimize your processes and ensure excellent results, prioritize high-quality membranes that meet your specific needs.
For any questions or to learn more about our offerings, visit silicone-membranes.eu.